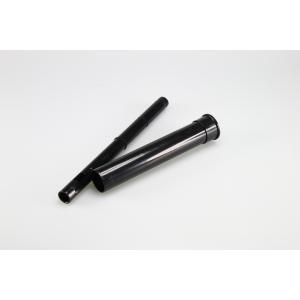
Add to Cart
Product Name: | Spare Tooling For Plastic Injection Mold | Material: | 1.2343,1.2311, H13, SKD61, S136 |
---|---|---|---|
Surface Finish | Line Polishing | Color: | Natural |
Standard: | HASCO Copy | Term: | FOB Shenzhen |
In-house mold design and building capabilities, complete supply chain solutions.
Customers can choose from a vast selection of thermoplastics and thermosets that best suit their needs for strength and function. We’ve worked with many types of resins, including: plasti
Material type we can do:
mc injection molding,injection mold plastic
Material type | Abbr | Description and typical applications |
Acrylonitrile Butadiene Styrene | ABS | Opaque & tough / Phones & computers |
Polypropylene | PP | Opaque & tough / Beer crates |
Polystyrene | PS | Clear & Brittle / Toys & model kits |
Polystyrene High Impact | HIPS | Opaque & tough / Toys & model kits |
Acetyl | POM | Natural & very tough / Gears & bearings |
Polycarbonate | PC | Clear and very tough / Street lamp covers & safety helmets |
Plasticized Polyvinylchloride | PVC | Opaque & flexible / Shoe soles & electrical insulation |
Polyamide 6 | PA6 | Opaque & very tough / Bushes, bearings & curtain fittings |
Polyamide 6.6 | PA6.6 | Opaque, tough and rigid / Housings & handles |
Polyamide 12 | PA12 | Opaque tough & rigid / Air filters & spectacle frames |
Polyethylene low density | LDPE | Waxy tough & flexible / Kitchenware & sealing lids |
Polyethylene high density | HDPE | Waxy tough & stiff / Crates & chair seats |
Thermoplastic Elastomer | TPE | Flexible & tough / Seals & washers |
Thermoplastic Rubber | TPR | Flexible & tough / Seals & washers |
Acrylic | PMMA | Transparent & Brittle / Lenses & car lights &Display |
Polystyrene General Purpose | GPPS | Clear & brittle / Ball point pen barrels |
Polyphenylene Sulphide | PPS | Brown & very strong / Guides & bearings |
Polyphenylene Oxide | PPO | Tough & stable / Electrical parts |
Rigid Polyvinyl Chloride | UPVC | Opaque & tough / Fascia fittings & guttering |
Styrene Acrylonitrile | SAN / AS | Clear & brittle / Table & picnic ware |
Polyether Sulphone | PES | Clear & tough / Metal replacement parts |
Cellulose Acetate | CA | Clear & tough / Spectacle frames |
You can choose plastic finishes as follow:plastic injection molding,injection mold plastic
· Metallization (chrome, gold, silver)
· Painting (hand, screen, automated)
· Vacuum plating
· Lithography
· Custom texturing
· Hydrographics
Detail
plastic
Material | Rubber: NBR, SBR, HNBR, EPDM, FKM(VITON), MVQ, FMVQ, CR, NR, SILICONE, etc… Plastic: ABS, PE, PA6, PA66, PP, PC, POM, PMMA, EVA, PU, PVC, TPR, TPE, TPU, etc... according to the customers' requirements |
Dimension | According to the customers' drawings |
Performance requirements | According to the customers' requirements (Tensile strength, elongation, compression set, high temperature resistance, low temperature resistance, ozone resistance, density and so on) |
Plastic parts color | Black, white, any other colors as per Customers’requirement or as per RAL code. |
Plastic parts surface | Painting, screen print, polishing, vacuum plating, chrome plating etc. |
Mold life | 1,000,000 shots |
OEM | OK |
Applications | Industrial plastic parts, home appliances, Automobiles, stationery, gifts,medicines etc. |
Rapid Development line | A. From drawing, new tool design to mold support and samples. B. Prototype mold, usually in 7 days; C. Mass production mold, usually in 1~2 weeks. |
File format used | Solidworks,Pro/Engineer,Auto CAD,PDF,JPG ect |
The most common problems in overmolded cable assemblies center around overmolding approaches that limit the molding and assembly process parameters such that producing an acceptable range of parts is difficult. This is where the approach to overmold tooling design comes together. It is important to integrate the cable assembly process, tooling design and injection molding process. Too often, these functions are segregated and the end result is parts that do not work. The design of overmold tooling that facilitates interchangeable sections, and therefore modular molds, is often a great help in faster response to molding issues and lower tooling costs overall.
The familiar cry of "the molds don't work" often is the result of incomplete design of the overmold tooling relative to the cable assembly process, and utilizing a customer design that combines components, materials and processes that are inherently incompatible. Just as successful cable assemblies begin with good crimps, successful overmolded parts start with good mechanical stability between the components being molded. Once there is mechanical stability, the opportunity to focus on achieving optimum output from the design can be developed. Here, the combination of cavity design and part loading helps to determine the right configuration. Develop a multifaceted design team with a working knowledge of cable assembly and termination, overmold tooling design and injection molding processes. Approach the tooling equation from a less is better approach, and look at the total cost, including tooling, projected over the life of the part.